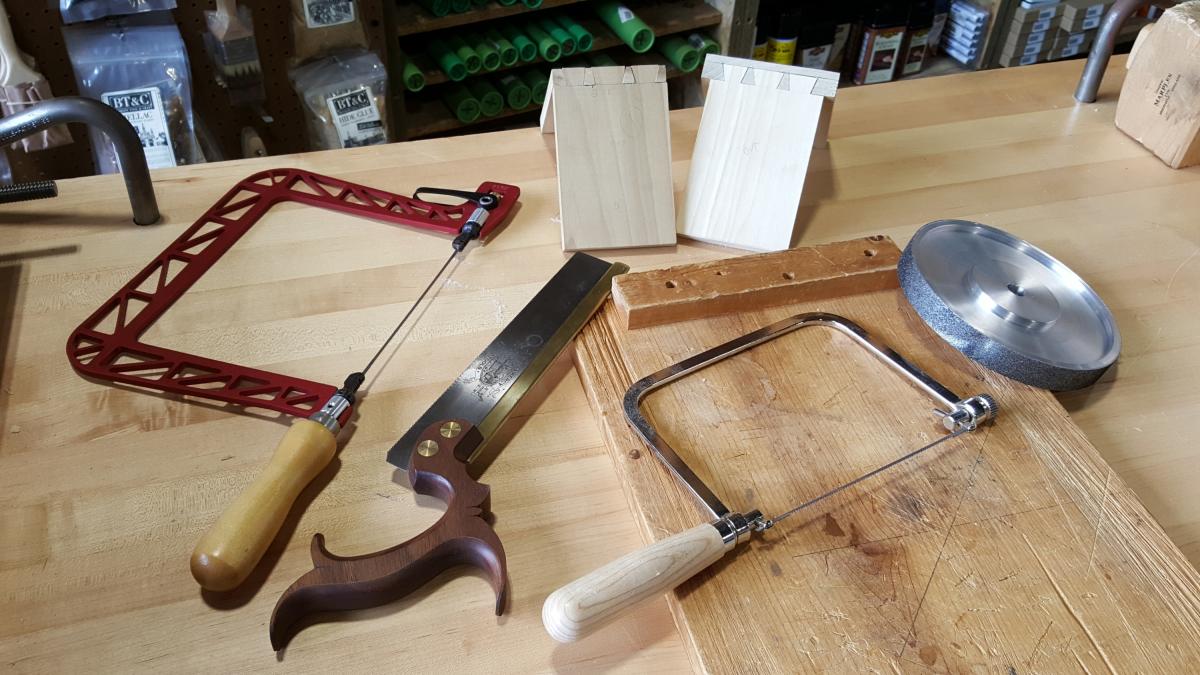
This is Part 3. Part 1 is here. Part 2 is here
I've been working with wood since I was a kid. I took my first woodworking class at the 92nd Street Y when I was 6 years old. I've been taking classes and building stuff for over 35 years. For the last 17 I have been working at Tools for Working Wood. In that time, new tools and new techniques have come on the market. By and large I have ignored them in my personal work. However, I haven't ignored everything, and my methods of work have in certain areas changed dramatically for the better. I've broken up my list of ten things into three posts so I don't drone on and on here.
When I was I school, we would go out of our way not to grind anything. The grinding wheel was smooth, the sharpening jig was very hard to set up, and without exercising extreme care, burning the tool was the norm. Around 2003 or so, Barry Iles of Ashley Iles Edge Tools taught me how to grind like a pro. (I later wrote about this technique for Fine Woodworking magazine and on my blog. This was a revelation for me and I started hollow grinding everything. Most of my sharpening kit became unnecessary. I helped develop the Norton 3X wheels which use seeded gel technology for cooler grinding, and they were a big step forward too. Then a few years ago I heard about CBN wheels, which are aluminum wheels with CBN crystals bonded to them. This innovation was great. The new wheels ran cooler than the 3X wheels and required no maintenance. No dressing or anything! The only trade-offs that I can think of are that they cost a lot more than regular wheels; you can't use them for non-ferrous metals (they clog); and they don't have the crown that Barry Iles showed me makes grinding so easy. I had some crowned CBN wheels made and I was sold! The non-ferrous problem is solved by changing only one wheel on a grinder to CBN. The cost is still, understandably, a deterrent to lots of people, but if you have the budget I cannot imagine why you would not switch.
The next couple of items are all tied together in how I make joints now vs thirty years ago.
Pistol Grip Saws
I learned on gent's saws. Gent's saws have two advantages for beginners: they are inexpensive and they are easier to use than a lot of other options. By easier to use, I mean easier to saw straight with. However, the straight handle, which great for enabling sawing straight, does so at a compromise is speed and comfort. I currently use our Gramercy dovetail saw. It seems as easy to use as a gent's saw but with more comfort and power.
Cutting Waste with a Coping Saw
I was taught to chisel dovetail waste out. It's not hard. I know a lot of people who use fret saws to remove most of the waste of a through dovetail. It does make chiseling to the final base line a little easier, but I have always hated the fragile blades. Using a bow saw or a coping saw isn't as straightforward. You kind of have to do two cuts, and the baseline needs to be chiseled anyway. It's a lot faster than using a fretsaw and you don't break blades. Start on one side of the waste, a little in from the edge of the joint, saw diagonally down until you touch - but not cut into - the saw kerf on the opposite side of the joint. Then, starting on that side, cut straight across the waste, removing the bulk of it all. BTW, the secret to a good coping saw is a sharp good blade.
No Layout Dovetails
When I studied woodworking, we measured compulsively. We spent weeks carefully cutting to a line and then chiseling out. As I have written in recent blogs, I discovered that the less I thought about it, the easier it was to saw straight. It was a huge wake-up call for me. My new model is treating sawing dovetails and everything else like a sport, in which practice, follow through, and instinct trump compulsive attention to analytic detail. This is the approach I use in my classes when I taught more. We have had great success, and I can't imagine going back thee other way. It's true that there are some joints that do require compulsive measurement - a twisted dovetail for example - but once the hand skill are practiced, and the muscles know what they are doing, scribe lines and measurement became a welcome guide instead of an impossible standard to meet.
Has your woodworking changed over the years too? I welcome your comments.
New week - Number 10.
|
Trust me! Measurements are essential but learning to trust your eye is the key to fair curves and pleasing proportions.
Sleep on it! When making a critical design decision or fine tuning a mock-up to be "just right" walk away when you think it's perfect and come back later with a fresh and clean perspective to confirm your decision.